Pattern Matching Inspection System
Transforming industries with our pattern-matching inspection
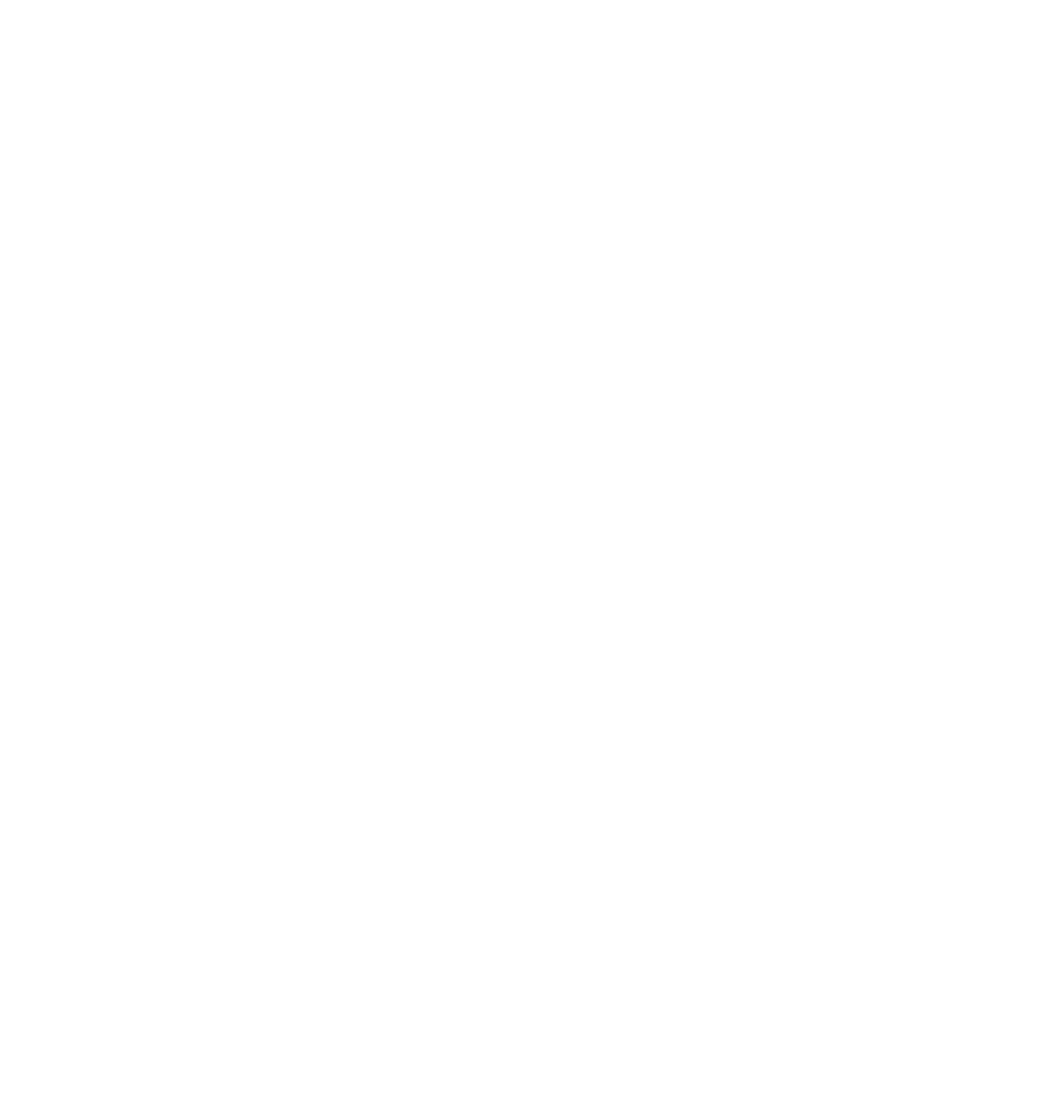
Uplifting standards with our pattern matching inspection
Empowering perfection with our system
What is pattern matching inspection?
Basically, pattern matching is a roadmap to automate the process of locating a pattern in an image using a machine vision techniques, adding into that it locates a part in a field of view and recognizes its availability or non- availability. It has proven to be useful for finding patterns in medicine and can be a crucial tool in other scientific applications.
This method is widely used in various industries, including manufacturing, electronics, and quality assurance, to detect defects, irregularities, or deviations in products.
What is the use of the pattern matching inspection?
The use of pattern matching inspection is used in applications where you want to ensure that the correct product is going well on the production line and communicates well.
OptoPixel’s pattern-matching inspection is used to find objects and easily identify models that are translated, rotated, and scaled to sub-pixel preciseness. Pattern matching inspection includes high-speed contour matching pattern recognition, which includes a powerful- pattern training wizard, that activates the precise and repeated setup of systems and by checking patterns on packs, parts, sub-assemblies, and components to verify the faults.
What is the use of the pattern matching inspection?
The use of pattern matching inspection is used in applications where you want to ensure that the correct product is going well on the production line and communicates well.
OptoPixel’s pattern-matching inspection is used to find objects and easily identify models that are translated, rotated, and scaled to sub-pixel preciseness. Pattern matching inspection includes high-speed contour matching pattern recognition, which includes a powerful- pattern training wizard, that activates the precise and repeated setup of systems and by checking patterns on packs, parts, sub-assemblies, and components to verify the faults.
What to expect from a pattern matching inspection?
01
High accuracy and precision
Pattern-matching inspection systems are designed to provide accurate and precise comparisons between the observed patterns and references. Expect a high level of reliability in identifying even subtle variations, ensuring greater control of quality
02
Detects defects
One of the primary purposes of pattern-matching inspection is to detect defects in the ideal pattern. This can include variations in shape, size, color, texture, or any other visual characteristic specified in the references submitted
03
Quick inspection
Pattern-matching systems are known for their speed and efficiency. Expect rapid image processing and analysis, enabling
real-time inspection of products on the production line. This efficiency contributes to increased throughput and faster decision-making
Benefits of pattern matching inspection system
Detects defects in
a complex pattern
Stands by the
quality standards
Higher speed in
large production
Provides a
cost-effective solution
Lower down
the false rejections
Solution with continuous improvement
What do we provide?
In terms of offering Pattern Matching Inspection Solutions,
we at OptoPixel are unbeatable.
With us, you can relish a top-notch, custom-fit, and cost-effective vision inspection system that reduces the inspection time and ensures a premium-grade final product.
- Verification of the position and orientation of a part
- Identifying or detecting the missing or duplicate parts
- Easy handling of reflection-prone surfaces
- Assessment of the product type through the existing data
- Verification of the components present in assembled part
- Identifying, picking, rotating, and placing the operations via robot guidance
- Audit and integrity reporting
- Verification and integration of inline machine
- Remote software aid at all convenient hours
- Evaluating whether the accurate nut, bolt, or screw head is attached