Bearing Inspection System
Bringing perfection in the form of a bearing inspection system
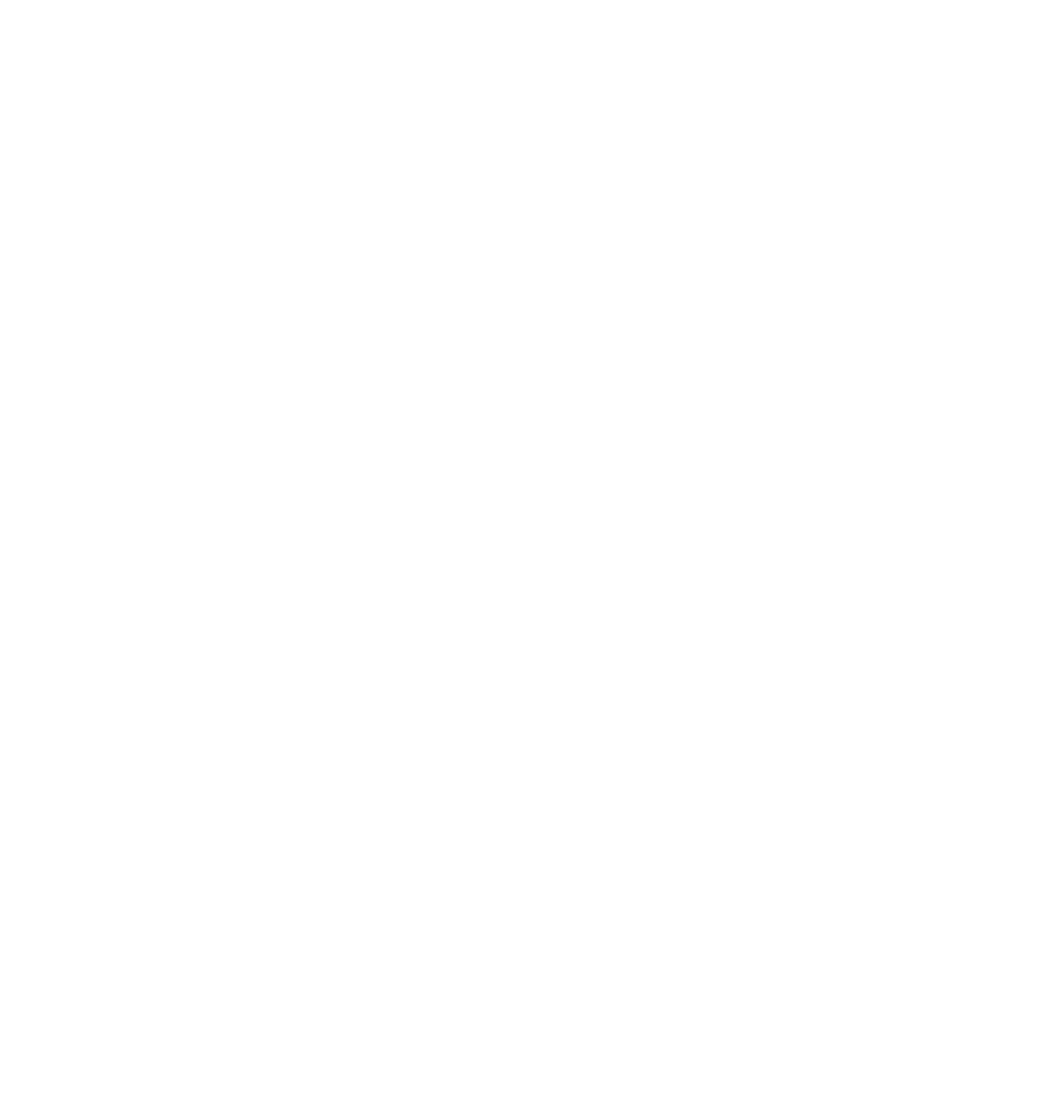
We are here to revolutionize reliability with our inspection system
The future of inspection system
What is bearing inspection system?
Bearing is a very critical component when it comes to the automotive industry. Defects in the process of making the vehicles are unfinished surfaces, scratches on machined surfaces, etc can occur due to either improper handling
OptoPixel’s bearing inspection system is a trained tool trained to overcome these defects reliably. The bearing surface and bearing rollers both have a significant impact on the installation performance, use, quality, and life of the bearing
Why is bearing inspection important?
Bearings, as an integral part of various mechanical systems, bear the responsibility of facilitating smooth rotation and minimizing friction. Regular inspection of bearings is essential to detect potential defects, wear, or misalignments that could compromise their performance and, consequently, the overall functionality of the machinery they support. Timely and thorough bearing inspections contribute to preventing unexpected failures, reducing downtime, and extending the lifespan of equipment
Why is bearing inspection important?
Bearings, as an integral part of various mechanical systems, bear the responsibility of facilitating smooth rotation and minimizing friction. Regular inspection of bearings is essential to detect potential defects, wear, or misalignments that could compromise their performance and, consequently, the overall functionality of the machinery they support. Timely and thorough bearing inspections contribute to preventing unexpected failures, reducing downtime, and extending the lifespan of equipment
The 3 important rules of bearing inspection
01
02
03
Benefits of bearing inspection system
Enhanced level
of performance
Maximized level
of production
Detection
of defects
Real-time monitoring
and analysis
Saves cost on a
huge scale
Highly enhanced
safety measures
What do we provide?
OptoPixel is the leading Bearing Inspection System Provider.
We offer top-notch Bearing Inspection Systems for a wide range of industries.
Our highly advanced Bearing Inspection System has an impressive list of features.
- Verification of the number of balls or rollers
- Audit and integrity reporting
- Handling of highly reflective surfaces
- Verification of components present within the assembled bearing
- Detection of duplicates or missing parts
- Inline machine verification and integration
- Inspection of the surface of the bearings for cracks, rusts, scratches, etc.